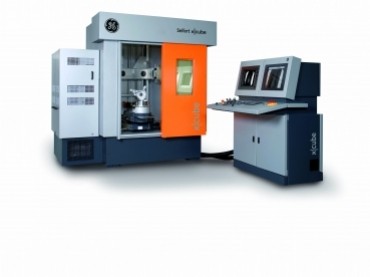
The x|cube series is a highly versatile industrial X-ray system family for radioscopic spot tests and inspection of automotive or aerospace samples such as light metal castings, steel components, plastics, ceramics and special alloys with 160, 225 or 320 kV. Its design allows a great flexibility in applications such as production, incoming inspection, failure analysis or research & development. The ease of operating and programming and Flash!FiltersTM image enhancement enable the user to make the correct inspection decisions. Optional Computed Tomography allows even 3D inspection.
Designed for a wide application range depending on the inspection task, two x|cube models are available: the x|cube Compact and the x|cube XL.
Each model is offered in a 160 kV and a 225 kV version, comes with a choice of workpiece holding tables and can handle workpiece dimensions of up to 600 mm diameter and 900 mm height, and an overall weight of up to 100 kg. The XL model has a larger X-ray protection cabinet and is, thus, suitable for the X-ray inspection of parts with dimensions of up to 800 mm diameter and 1,500 mm height. To provide an inspection solution for the increasing demand to inspect large light metal parts of up to 300 kg or high absorbing steel parts such as turbine blades, the x|cube is now also available in an advanced 320 kV version coming with maintenance free high voltage plugs for high productive, low maintenance inspection on the production floor.
Key Features and Benefits
- Wide application range from automotive’s fast throughput requirements with 30 fps at full resolution to aviation’s casting requirement of premium resolution
- Visual real-time inspection combined with optional 3D CT capability
- Simple loading with extractable parts manipulator for parts weighing up to max. 100 kg (300 kg at 320 kV version)
- Max. sample size 600 x 900 mm (800 x 1,500 x|cube XL)
- Patented extremely low vibration C arm manipulator, flexible swivel angle of +45° to -45°
- Robust design and intuitive operator guidance with X-Touch® control
- Panel Inspection task programming with teach and learn functions
- Automated defect recognition (ADR) for high sample throughput
- DICONDE standard compliant digital image analysis and data management
- Short failure detection time with GE’s Flash!FiltersTM image optimization option
- Optional basic automatic defect recognition for aluminum casting defects
- Optional CT functionality for virtual 3D sections and quantitative porosity analysis
- All relevant hardware and software components are GE technology Reduced maintenance – lower operating costs
– See more at:www.gemeasurement.com